LW series spiral discharge centrifuge is horizontal continuous operation, spiral continuous discharge sedimentation centrifuge. It is suitable for solid-liquid separation of all kinds of suspension in various industrial sectors, particle size classification liquid phase clarification and sludge dehydration (such as: polyoxyethylene resin, ammonium sulfite, barium carbonate, strontium sulfate, Lide powder, titanium dioxide, ore, China clay, kaolin, diatomite, starch, soybean protein, peanut protein, juice, beverage, vegetable oil, citric acid, waste oil purification, washing water purification, wine lees, movement) Physical fat, blood powder, power plant sludge, printing and dyeing sludge, paper sludge, natural gas desulfurization sludge, calcium carbide sludge, activated sludge, ammonia sludge, car wash sludge, alum sludge, drilling sludge, coal flotation waste, cryolite flotation liquid, etc.).
Hengrui automatic corrosion resistant LW decanter centrifugal dehydrator new centrifuge
Product Description
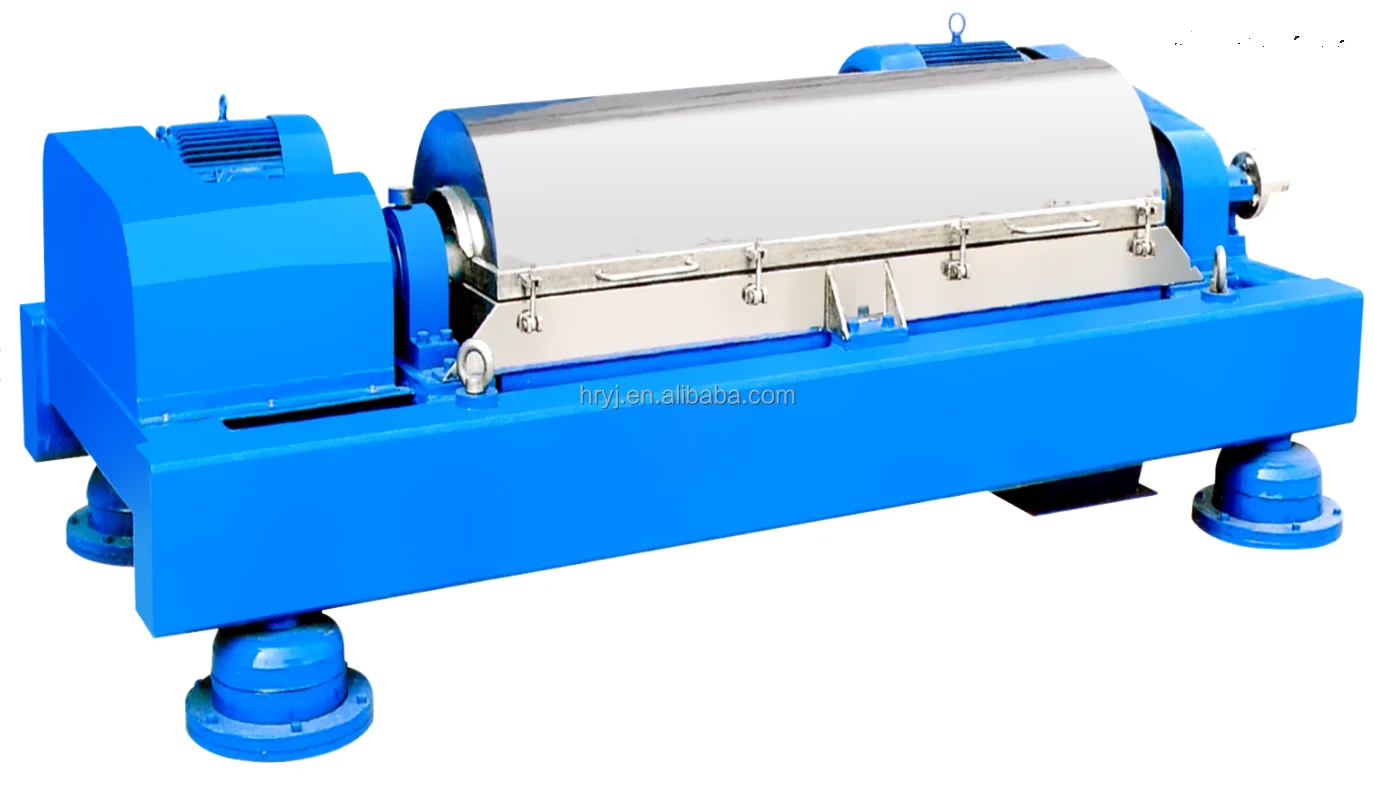
Product Structure
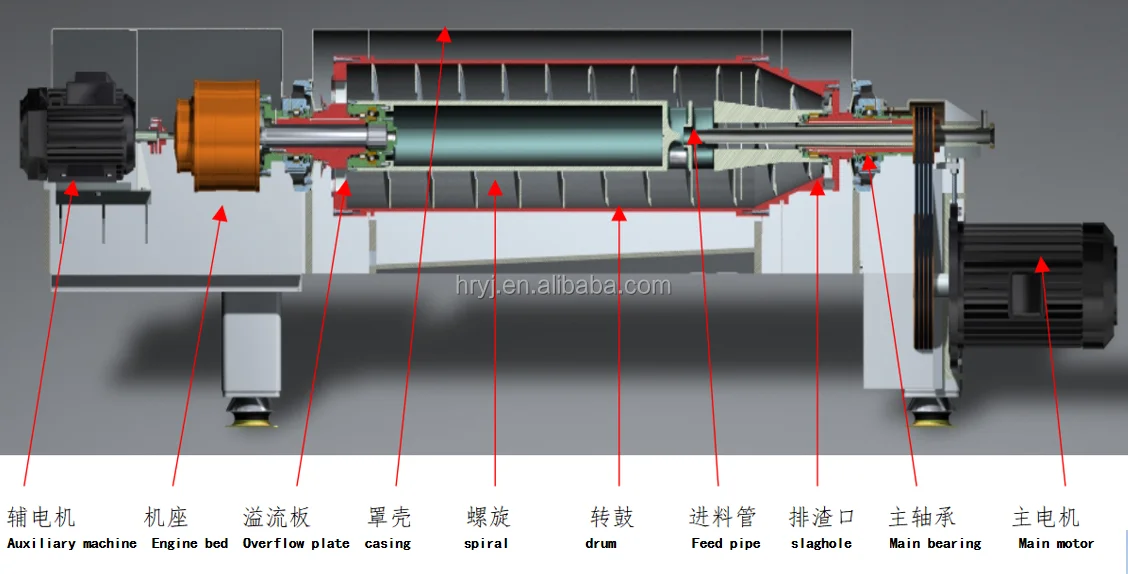
Working Principle
Decanter centrifuge is the abbreviation of horizontal screw discharge settling centrifuge. Decanter centrifuge in the form of mechanical differential is mainly composed of drum, screw, planetary gear differential, bearing seat, feed tube, frame, cover, main motor, auxiliary motor, electrical control system and various monitoring instruments. When the material enters the centrifuge drum chamber, it is driven by the high-speed rotating drum to rotate together at high speed, so the material will be subjected to strong centrifugal force. Due to the high density of the solid particles in the mixture, the centrifugal force is also large, so the solid phase will be dumped on the inner wall of the drum, forming a solid ring layer, while the density of the liquid phase is small, the centrifugal force is also small, and the liquid ring layer can only be formed inside the solid ring layer. Because the rotation speed of the spiral and the drum is different, the two have relative motion (that is, the difference in speed), so the spiral will push the solid deposited in the inner wall of the drum to the discharge port of the small end of the drum, and the liquid phase is discharged from the overflow port of the large end of the drum. The function of the differential is to form a certain speed difference between the drum and the helix.
Configurations
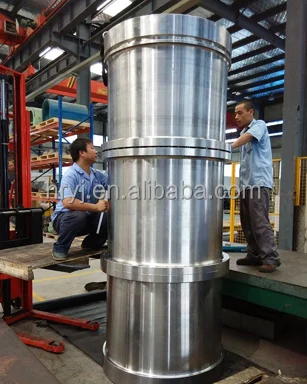
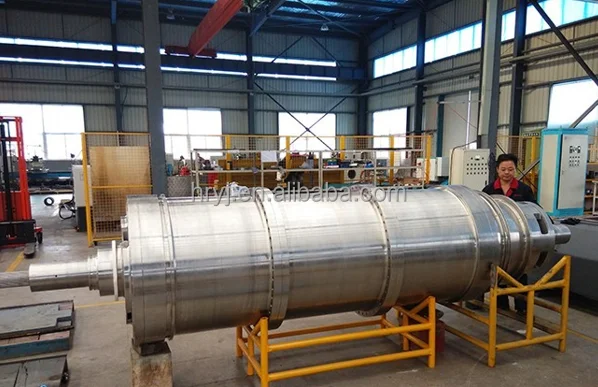
The drum material is 316L, (or 2205) and is made by centrifugal casting process. The inner surface of the drum is equipped with longitudinal wear-resistant strips, the material is SAF2205, this structure can effectively prevent the inner wall of the drum wear, increase the service life of the drum, and this structure is more conducive to solid phase discharge. The solid discharge port at the small end of the drum is inlaid with a replaceable high wear-resistant ceramic bushing to prevent the wear of solid materials on the slag outlet of the drum and improve the service life of the drum. The design of the drum uses finite element simulation and optimization design, and fully considers the key parameters such as the strength and vibration of the structure, so that the design can be optimized theoretically. The factory dynamic balance accuracy is G2.5.
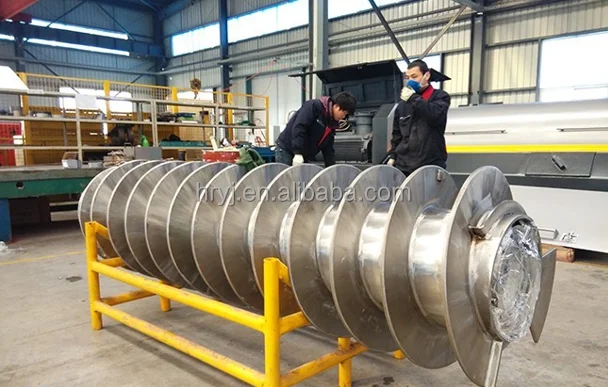
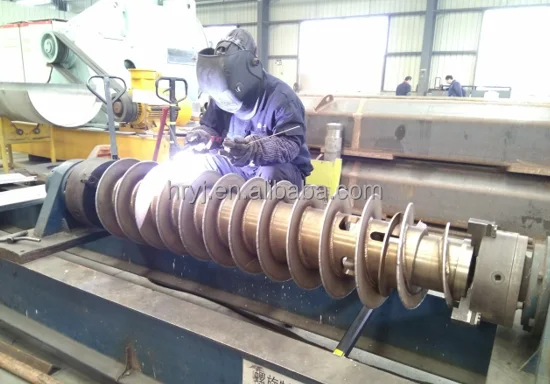
The screw (discharger) is made of 316L stainless steel, the cone end of the blade is inlaid with cemented carbide, and the rest is sprayed with cemented carbide. All spiral blades are installed and welded by hot pressing, which ensures the precision and strength requirements of spiral production. The top of the screw feeding chamber adopts a conical structure design to reduce the rebound after the impact of the material, improve the processing capacity, and avoid the phenomenon of plugging in the screw and feeding pipe. The screw also needs to undergo solution treatment and stress relief heat treatment to ensure its strength and aging strain stability. The factory dynamic balance accuracy is G2.5.
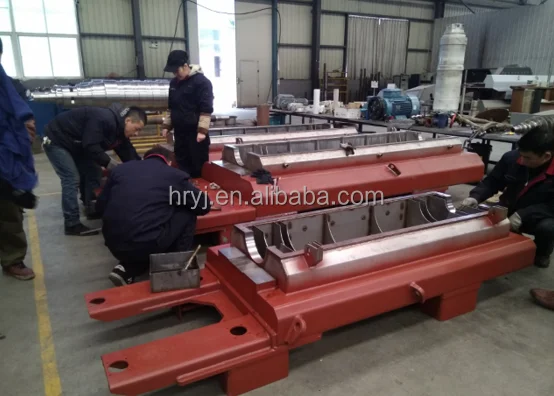
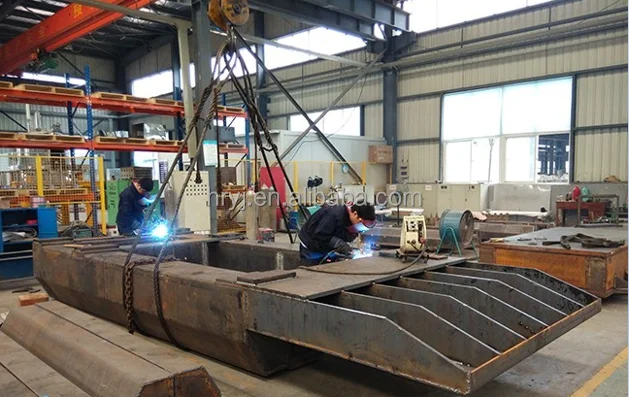
Frame material is made of high-quality carbon steel, all welded manufacturing, in the design through finite element simulation and simulation, to obtain the optimal structure form, namely vertical optimization structure, this structure can not only ensure that all the upper dynamic load, but also effectively reduce the vibration generated during the operation of the machine. The frame is connected to the shock absorber and can be easily installed directly on the concrete foundation.
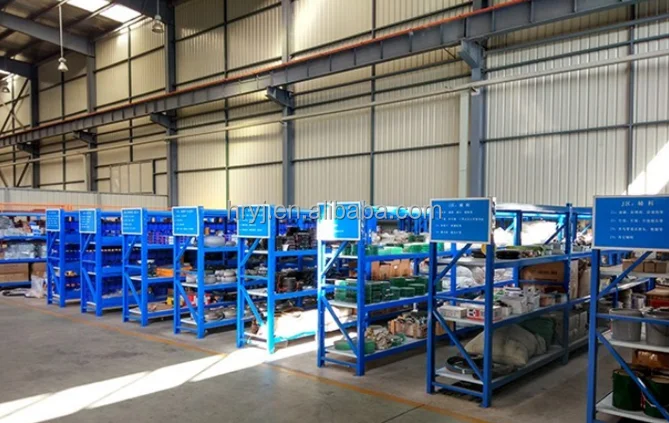
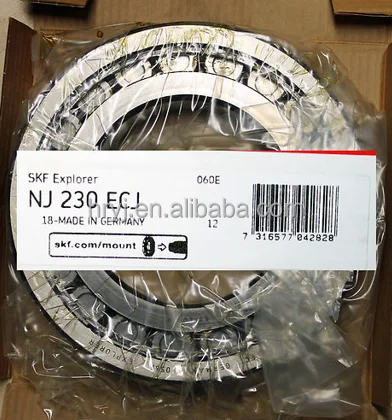
The main bearing adopts original imported SKF bearing. The main bearing of the big end of the drum is cylindrical roller bearing, which ensures that the equipment can run safely for a long time at high speed and bear large load; The big end of the screw is thrust bearing and cylindrical roller bearing, and the small end is cylindrical roller bearing or needle roller bearing, so that the screw can withstand higher pushing torque.
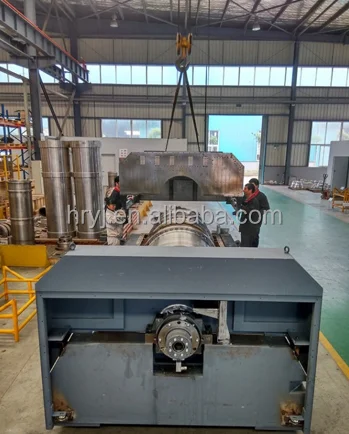
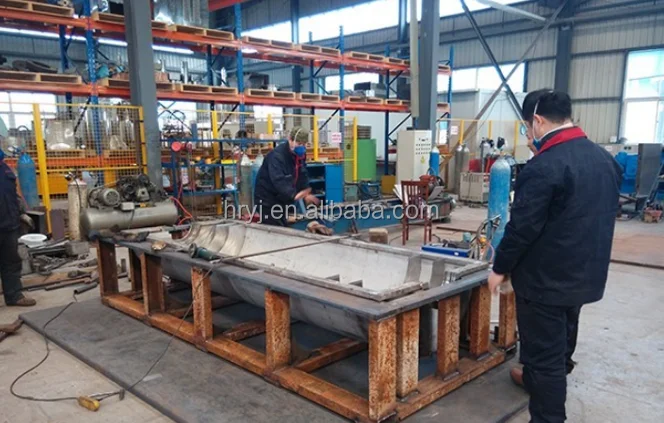
Case and safety cover: The case is made of 316L material, and the safety cover is made of stainless steel 316L material. Hengrui Company's unique open cover auxiliary device is used on the shell cover, so that the top cover of the centrifuge can be easily opened, closed and locked, which not only strengthens the requirements of safety, but also meets the simplicity of maintenance and repair. At the same time, the top of the shell is equipped with an online cleaning device, which can fully clean the drum discharge port and the inside of the shell.
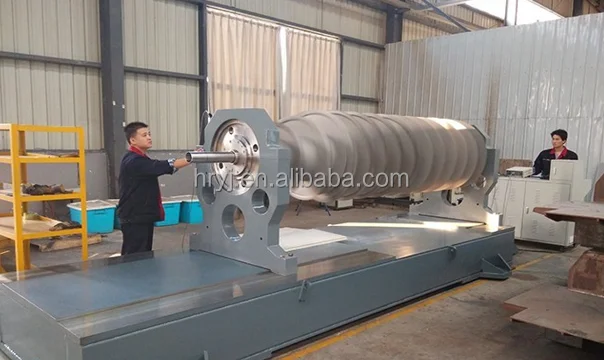
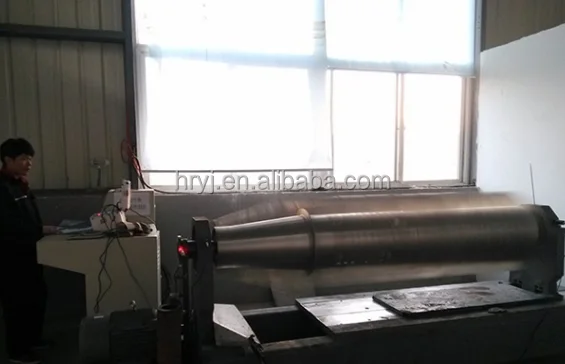
Full dynamic balance technology: Vibration control is one of the keys to manufacture decanter centrifuge, our company adopts full dynamic balance technology, that is, to the actual use of the speed into the action balance check and compensation, can effectively reduce the vibration of the machine, the maximum extent to remove or make up for the unbalance. This technical means can ensure that the company's decanter centrifuge in the vibration index is far better than the industry standard and peer level.
Production Site
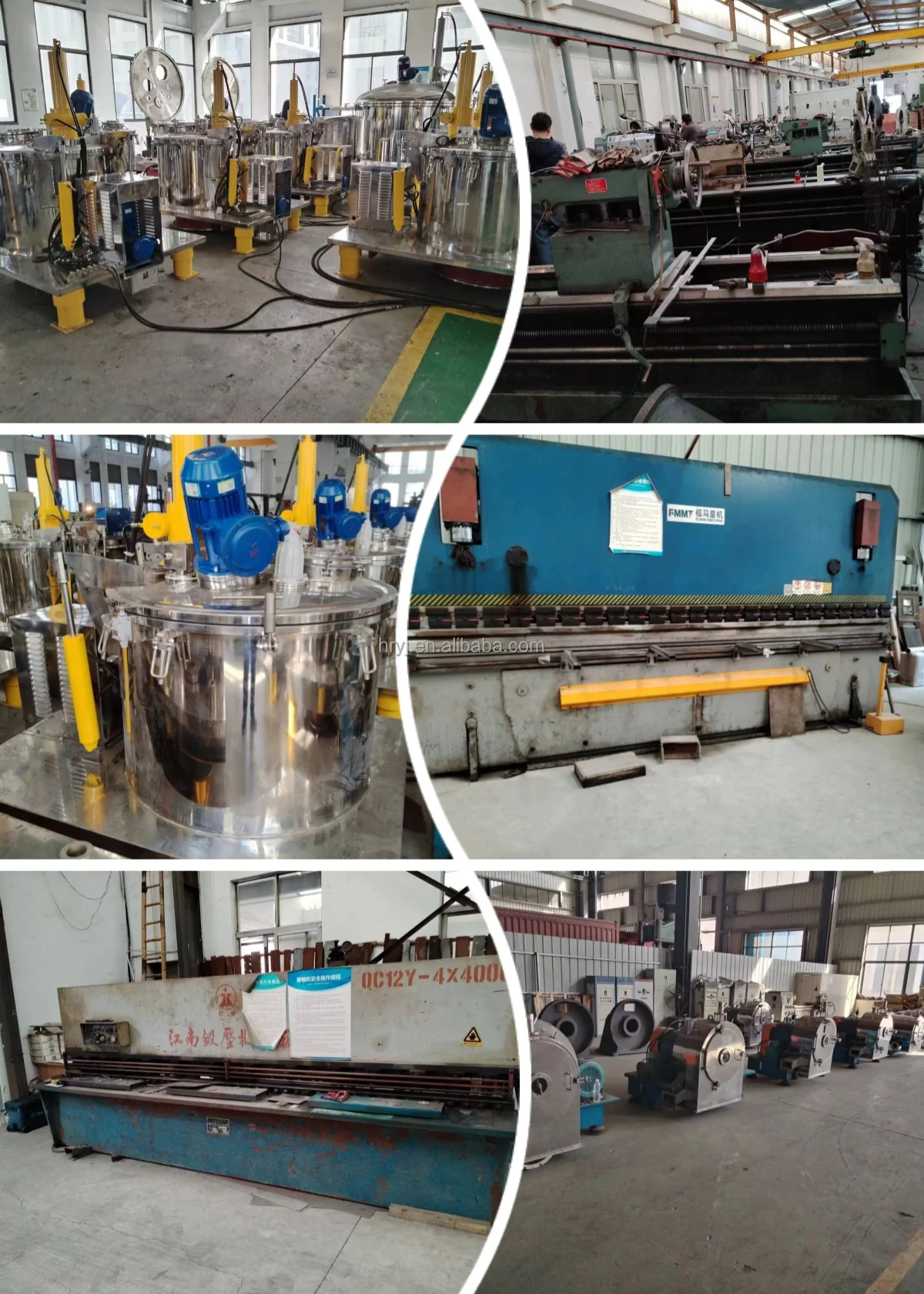
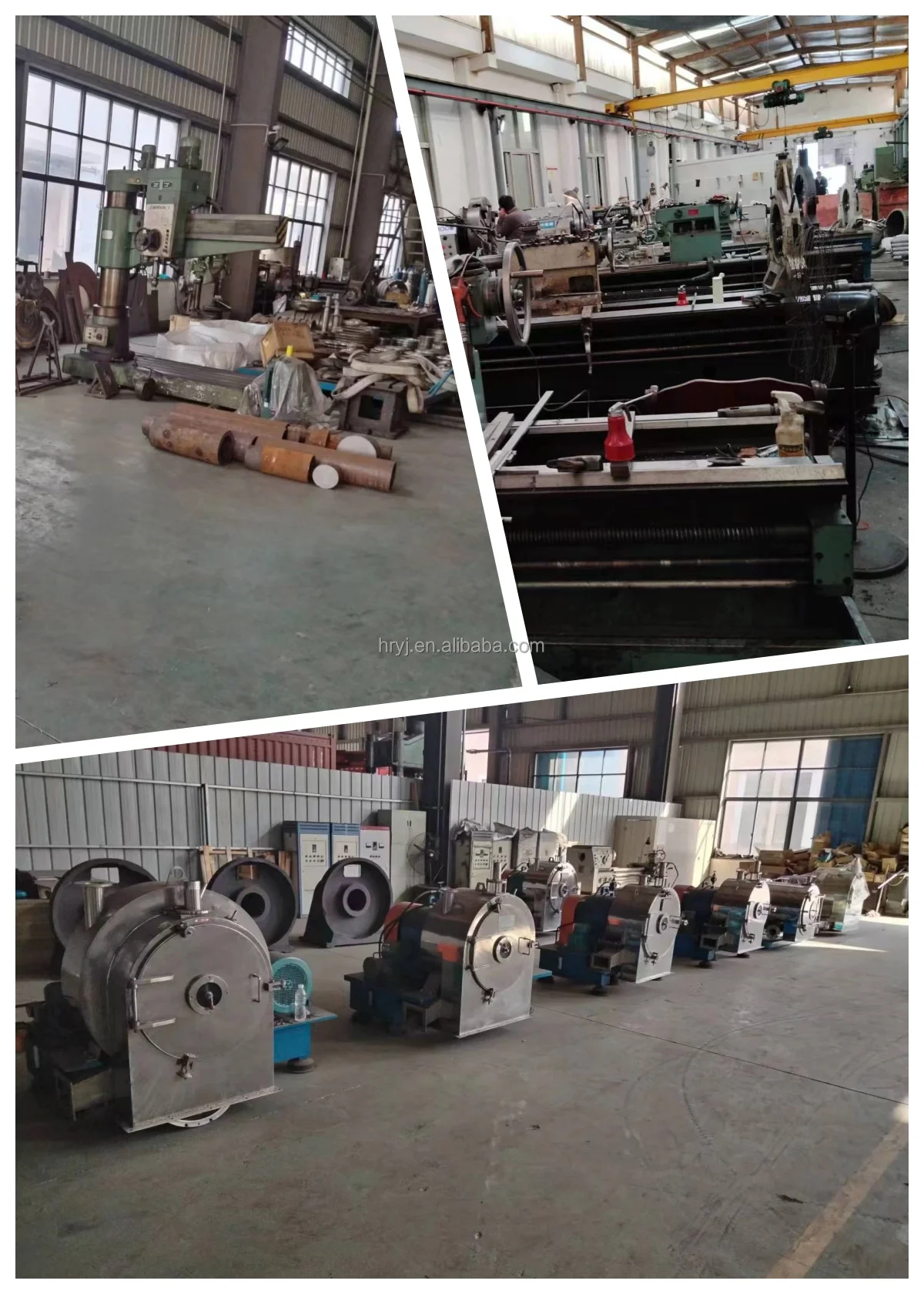
About Us
Zhangjiagang Hengrui Pharmaceutical Machinery Co., Ltd. is a vigorous company, founded in 2001, has its own strong factory, located in the beautiful Zhangjiagang city, Jiangsu Province, the factory area of 5000 square meters, the existing staff 60 people. The company mainly produces centrifuges, centrifugal extractors and other products, with an annual output of more than 500 sets and an annual output value of 30 million yuan.
Hengrui process control technology
We are committed to providing the most efficient and economical solid-liquid separation solutions to meet the needs of all customers. From the start of the project to the lifetime service of the equipment, customers will benefit greatly from our experts, advanced technical reliability and high quality override equipment.
Competitive power
Over the past 25 years, Hengrui Process Control Technology has become a leader in the separation equipment industry. The rich experience of our engineers comes from the realization of more than 2,000 products and more than 5,000 application cases, and more than 100 patents testify to our ability to innovate. This extensive empirical knowledge supports our methods and equipment recommendations, all of which are economical and performance optimized to meet your specific requirements.
- Description
- Related Products
Description
Product Description
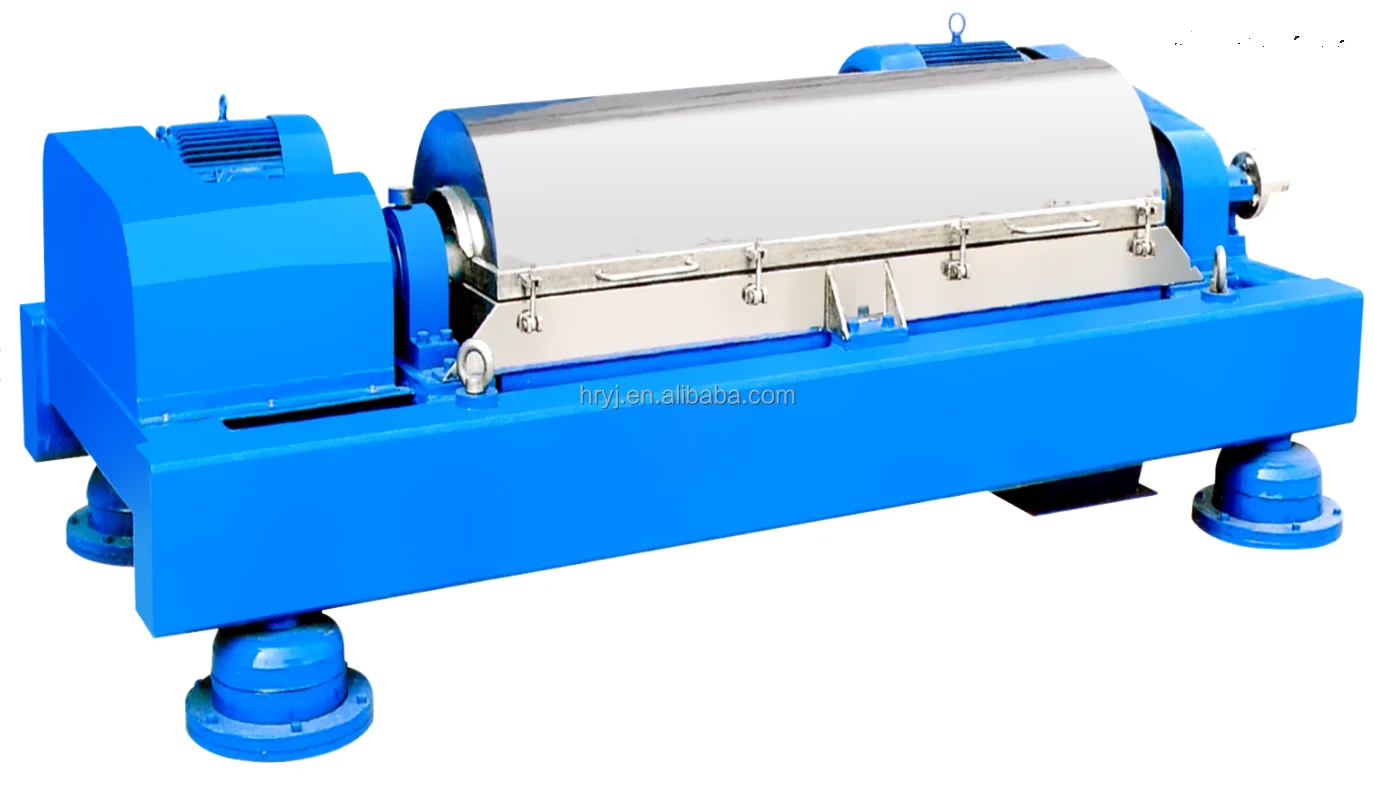
LW series spiral discharge centrifuge is horizontal continuous operation, spiral continuous discharge sedimentation centrifuge. It is suitable for solid-liquid separation of all kinds of suspension in various industrial sectors, particle size classification liquid phase clarification and sludge dehydration (such as: polyoxyethylene resin, ammonium sulfite, barium carbonate, strontium sulfate, Lide powder, titanium dioxide, ore, China clay, kaolin, diatomite, starch, soybean protein, peanut protein, juice, beverage, vegetable oil, citric acid, waste oil purification, washing water purification, wine lees, movement) Physical fat, blood powder, power plant sludge, printing and dyeing sludge, paper sludge, natural gas desulfurization sludge, calcium carbide sludge, activated sludge, ammonia sludge, car wash sludge, alum sludge, drilling sludge, coal flotation waste, cryolite flotation liquid, etc.).
Product Structure
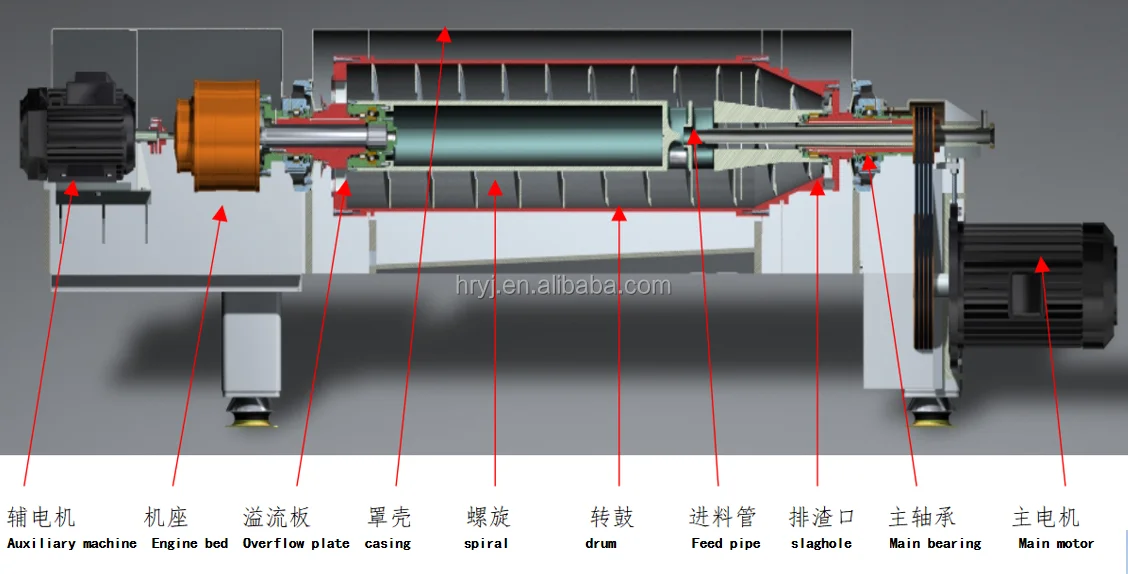
Working Principle
Decanter centrifuge is the abbreviation of horizontal screw discharge settling centrifuge. Decanter centrifuge in the form of mechanical differential is mainly composed of drum, screw, planetary gear differential, bearing seat, feed tube, frame, cover, main motor, auxiliary motor, electrical control system and various monitoring instruments. When the material enters the centrifuge drum chamber, it is driven by the high-speed rotating drum to rotate together at high speed, so the material will be subjected to strong centrifugal force. Due to the high density of the solid particles in the mixture, the centrifugal force is also large, so the solid phase will be dumped on the inner wall of the drum, forming a solid ring layer, while the density of the liquid phase is small, the centrifugal force is also small, and the liquid ring layer can only be formed inside the solid ring layer. Because the rotation speed of the spiral and the drum is different, the two have relative motion (that is, the difference in speed), so the spiral will push the solid deposited in the inner wall of the drum to the discharge port of the small end of the drum, and the liquid phase is discharged from the overflow port of the large end of the drum. The function of the differential is to form a certain speed difference between the drum and the helix.
Configurations
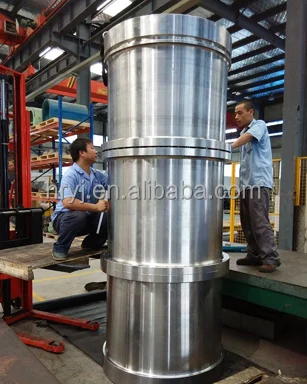
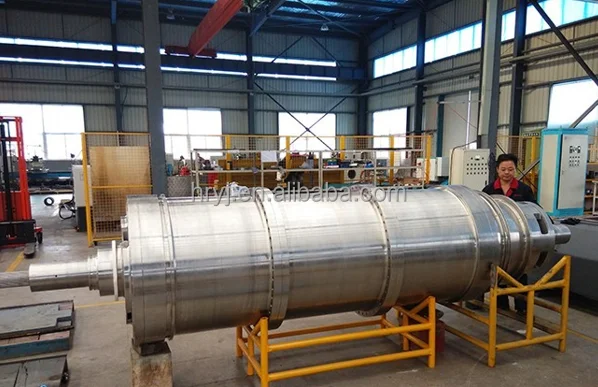
The drum material is 316L, (or 2205) and is made by centrifugal casting process. The inner surface of the drum is equipped with longitudinal wear-resistant strips, the material is SAF2205, this structure can effectively prevent the inner wall of the drum wear, increase the service life of the drum, and this structure is more conducive to solid phase discharge. The solid discharge port at the small end of the drum is inlaid with a replaceable high wear-resistant ceramic bushing to prevent the wear of solid materials on the slag outlet of the drum and improve the service life of the drum. The design of the drum uses finite element simulation and optimization design, and fully considers the key parameters such as the strength and vibration of the structure, so that the design can be optimized theoretically. The factory dynamic balance accuracy is G2.5.
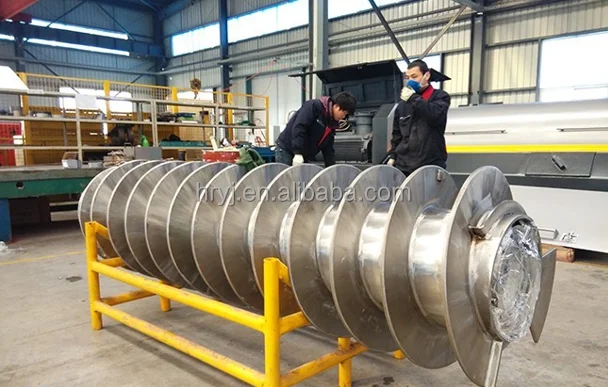
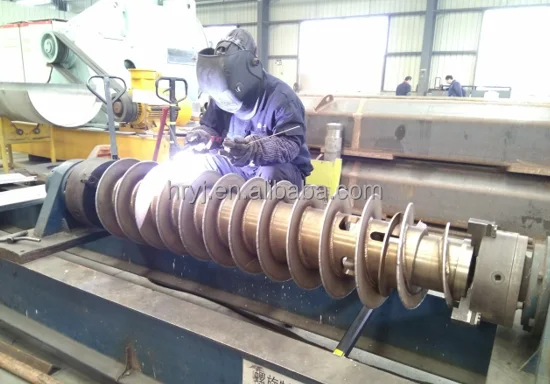
The screw (discharger) is made of 316L stainless steel, the cone end of the blade is inlaid with cemented carbide, and the rest is sprayed with cemented carbide. All spiral blades are installed and welded by hot pressing, which ensures the precision and strength requirements of spiral production. The top of the screw feeding chamber adopts a conical structure design to reduce the rebound after the impact of the material, improve the processing capacity, and avoid the phenomenon of plugging in the screw and feeding pipe. The screw also needs to undergo solution treatment and stress relief heat treatment to ensure its strength and aging strain stability. The factory dynamic balance accuracy is G2.5.
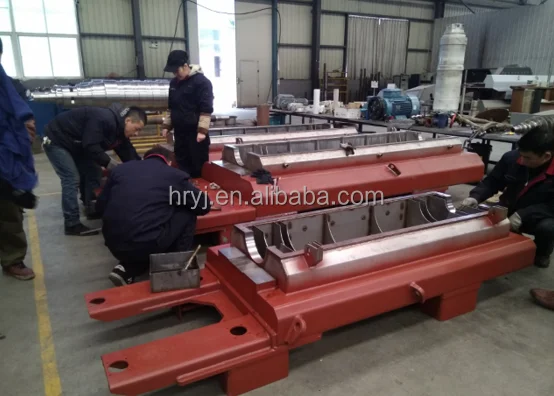
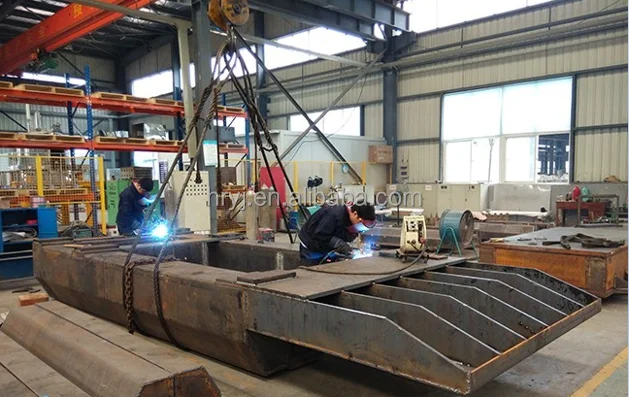
Frame material is made of high-quality carbon steel, all welded manufacturing, in the design through finite element simulation and simulation, to obtain the optimal structure form, namely vertical optimization structure, this structure can not only ensure that all the upper dynamic load, but also effectively reduce the vibration generated during the operation of the machine. The frame is connected to the shock absorber and can be easily installed directly on the concrete foundation.
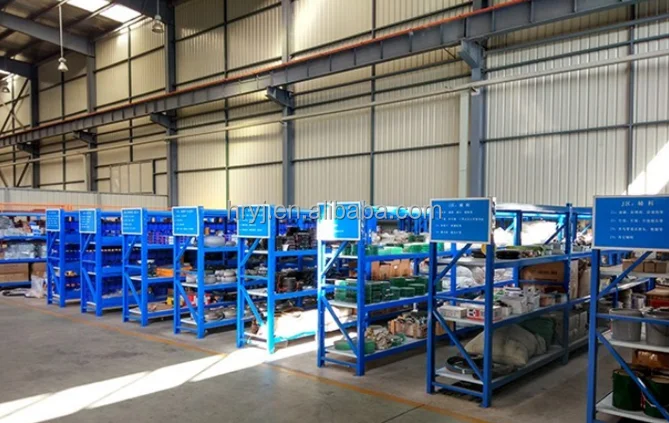
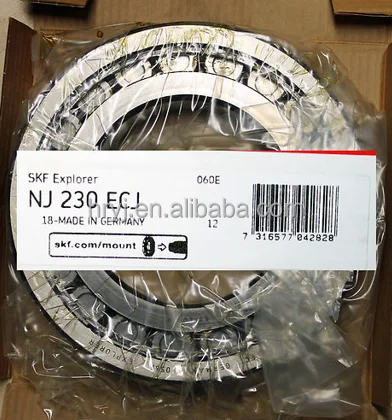
The main bearing adopts original imported SKF bearing. The main bearing of the big end of the drum is cylindrical roller bearing, which ensures that the equipment can run safely for a long time at high speed and bear large load; The big end of the screw is thrust bearing and cylindrical roller bearing, and the small end is cylindrical roller bearing or needle roller bearing, so that the screw can withstand higher pushing torque.
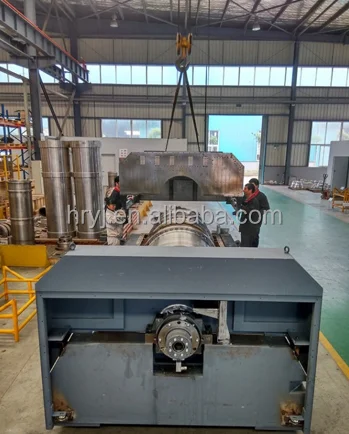
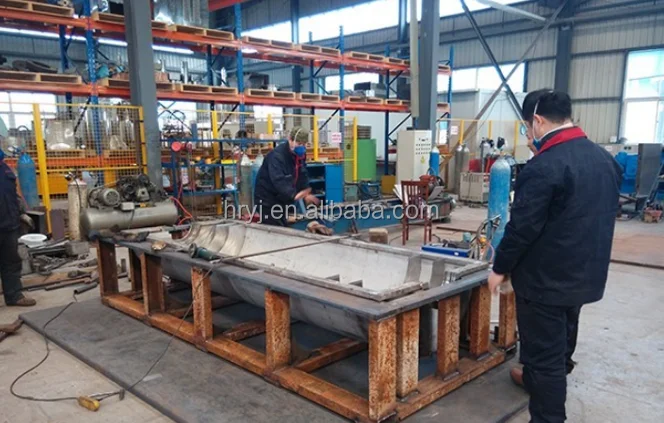
Case and safety cover: The case is made of 316L material, and the safety cover is made of stainless steel 316L material. Hengrui Company's unique open cover auxiliary device is used on the shell cover, so that the top cover of the centrifuge can be easily opened, closed and locked, which not only strengthens the requirements of safety, but also meets the simplicity of maintenance and repair. At the same time, the top of the shell is equipped with an online cleaning device, which can fully clean the drum discharge port and the inside of the shell.
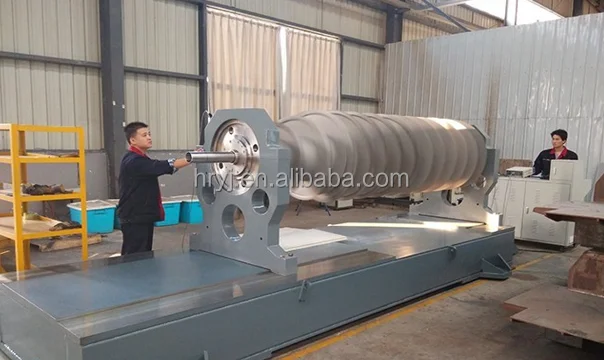
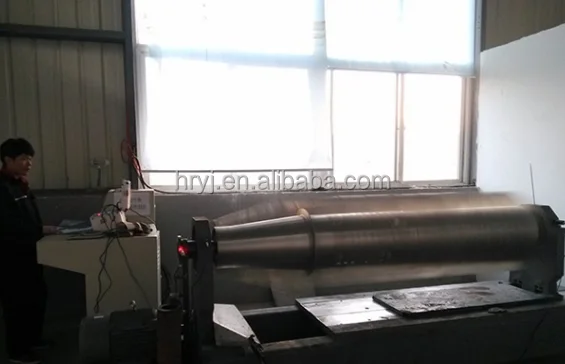
Full dynamic balance technology: Vibration control is one of the keys to manufacture decanter centrifuge, our company adopts full dynamic balance technology, that is, to the actual use of the speed into the action balance check and compensation, can effectively reduce the vibration of the machine, the maximum extent to remove or make up for the unbalance. This technical means can ensure that the company's decanter centrifuge in the vibration index is far better than the industry standard and peer level.
Production Site
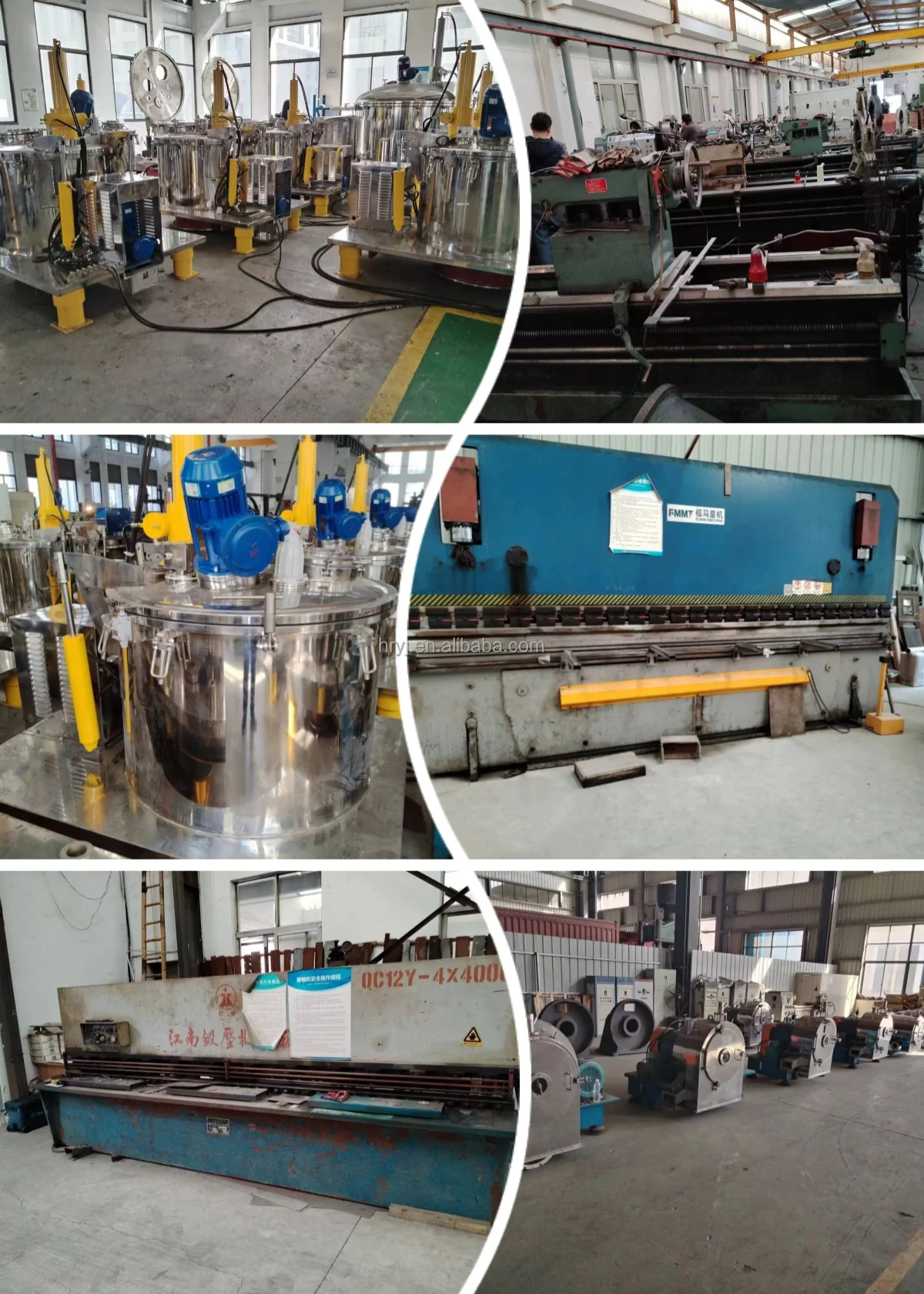
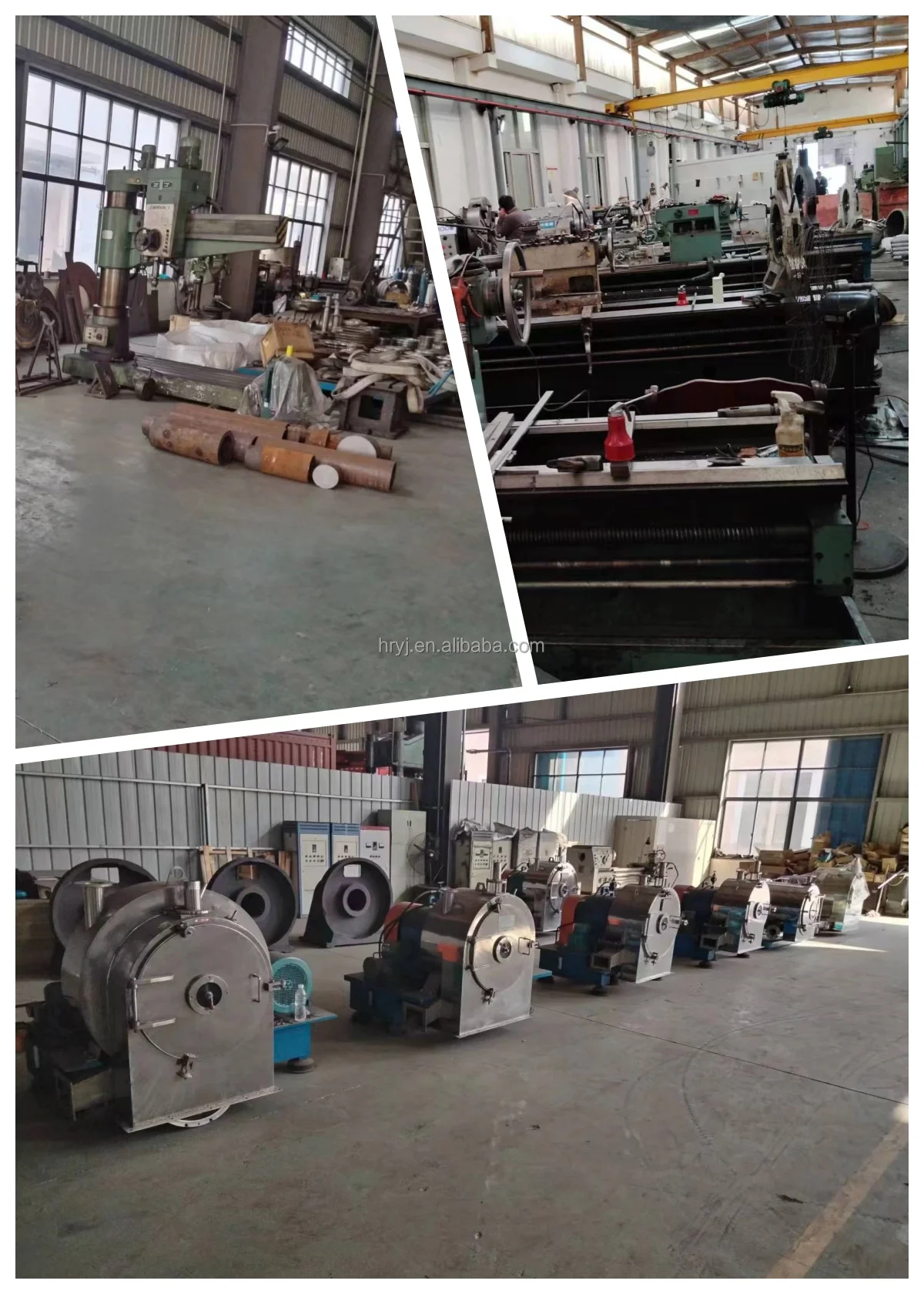
About Us
Zhangjiagang Hengrui Pharmaceutical Machinery Co., Ltd. is a vigorous company, founded in 2001, has its own strong factory, located in the beautiful Zhangjiagang city, Jiangsu Province, the factory area of 5000 square meters, the existing staff 60 people. The company mainly produces centrifuges, centrifugal extractors and other products, with an annual output of more than 500 sets and an annual output value of 30 million yuan.
Hengrui process control technology
We are committed to providing the most efficient and economical solid-liquid separation solutions to meet the needs of all customers. From the start of the project to the lifetime service of the equipment, customers will benefit greatly from our experts, advanced technical reliability and high quality override equipment.
Competitive power
Over the past 25 years, Hengrui Process Control Technology has become a leader in the separation equipment industry. The rich experience of our engineers comes from the realization of more than 2,000 products and more than 5,000 application cases, and more than 100 patents testify to our ability to innovate. This extensive empirical knowledge supports our methods and equipment recommendations, all of which are economical and performance optimized to meet your specific requirements.